Shallow-draught icebreakers present unique design challenges
The design of icebreakers, characterised by a relatively small draught in proportion to their main dimensions, requires particular attention. This specific design feature impacts many of the vessel’s core functions and parameters, which must be meticulously balanced to achieve the optimal performance.
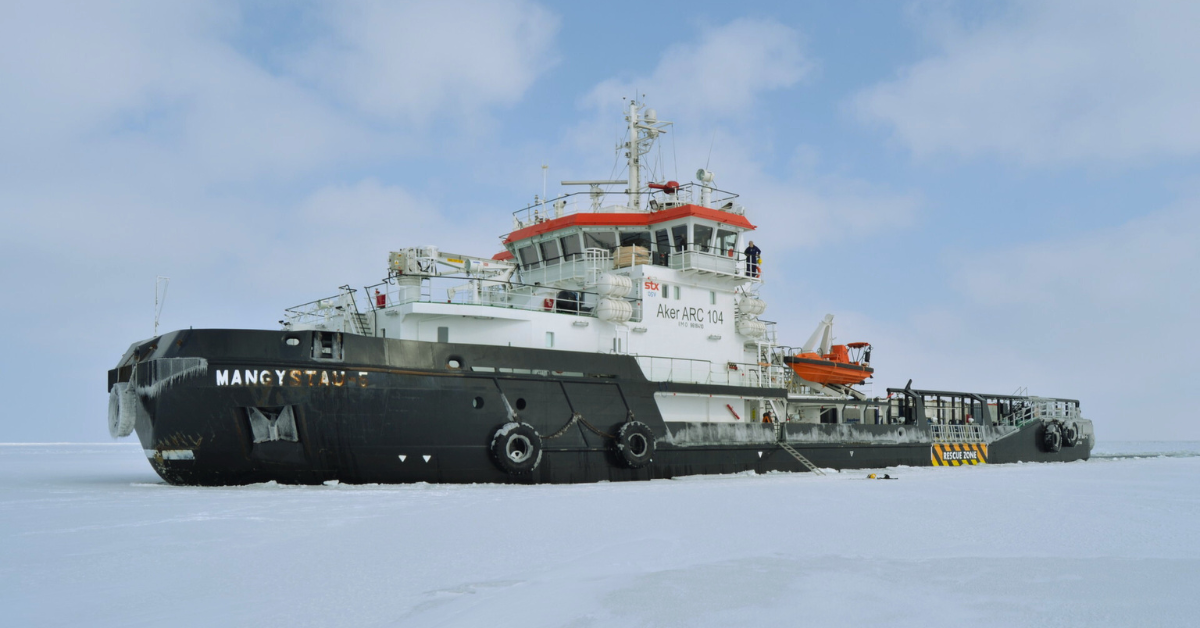
In naval architecture, certain fundamental principles guide the correlation between a vessel’s external dimensions and its draught for an optimal design. However, practical constraints in the intended operational area often impose limits on one or more dimensions, for example breadth in the Panama Canal, length limitation of a harbour, or draught to match water depth in the area of operation.
Shallow waters in freezing seas offer particular challenges for icebreaker designers. Here, the vessel’s primary dimensions must be adjusted beyond optimum configurations to meet the intended tasks, equipment, and endurance. These adjustments affect essential characteristics, including operability, manoeuvrability, open water speed, and icebreaking capability.
Every design choice matters
In Aker Arctic’s projects, icebreaking capability typically forms one of the foundations of the vessel’s design. The outline design then proceeds to defining the size, propulsion, and equipment to fulfil the specified level of performance criteria and other agreed tasks. Each decision in this process influences others, creating a delicate balance.
Senior Naval Architect Lars Lönnberg from Aker Arctic underlines that when designing shallow-draught icebreakers, even minor modifications can have significant effects.
“For instance, a shallow draught means that the propulsion system components must be relatively compact to fit the hull correctly and remain submerged. However, a smaller propeller diameter provides less thrust, which is a key feature in icebreaking,” he explains.
In shallow water, the vessel’s weight control is a crucial aspect of the design. It determines the equipment selection, endurance, and crew size; every feature that adds more weight. Also, the displacement relative to the vessel’s underwater side profile area can become substantial, impacting manoeuvrability.
“As a result, turning and other manoeuvres can be more challenging and must receive special attention during the design phase,” Lönnberg adds.
Providing space for ice rubble
Icebreaking in shallow water involves more than just breaking the ice, the draught and inertia; it also requires managing the ice rubble. Once the ice is broken, the resulting rubble needs adequate space to disperse. As the vessel moves in the channel, it pushes the ice blocks under the hull and in shallow waters the ice mass, though loose, may even reach to the bottom.
“Without sufficient space, the ice rubble can pile up on the seabed, potentially blocking the route and trapping the icebreaker,” notes Lönnberg.
Strong winds can exacerbate this issue by moving the broken ice, which may accumulate into ice jams and dams that stretch hundreds of metres, or deep ice ridges, hindering traffic and even causing flooding along riverbanks. In such situations, the vessel resistance may become so high that the vessel stops and cannot move forward even with ramming.
“Ensuring sufficient ice-clearing capabilities is therefore essential. Azimuthing propulsion has proven effective for clearing ice rubble and enhancing manoeuvrability, and recently developed azimuthing contra-rotating propellers (CRP) can further improve efficiency in shallow waters,” Lönnberg highlights.
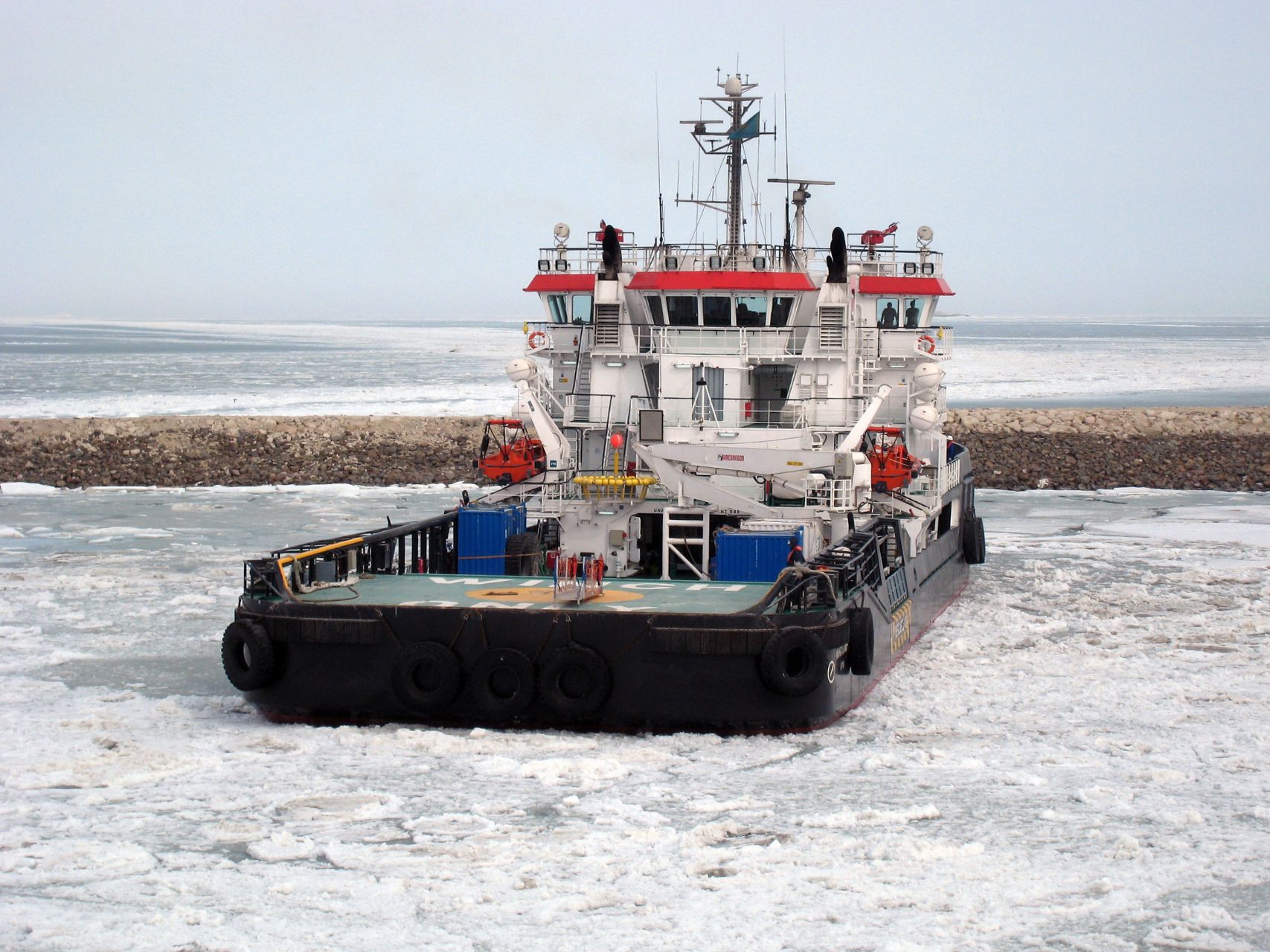
Brash ice grows with increased traffic
Part of the design process includes planning for adequate space to operate, for instance through dredging or creating passing lanes for traffic.
Aker Arctic has, over the years, conducted numerous studies on channel operation and brash ice formation since ship traffic in the Baltic Sea is partly in channels and, especially in the Saimaa Channel, much of the traffic is in restricted water areas.
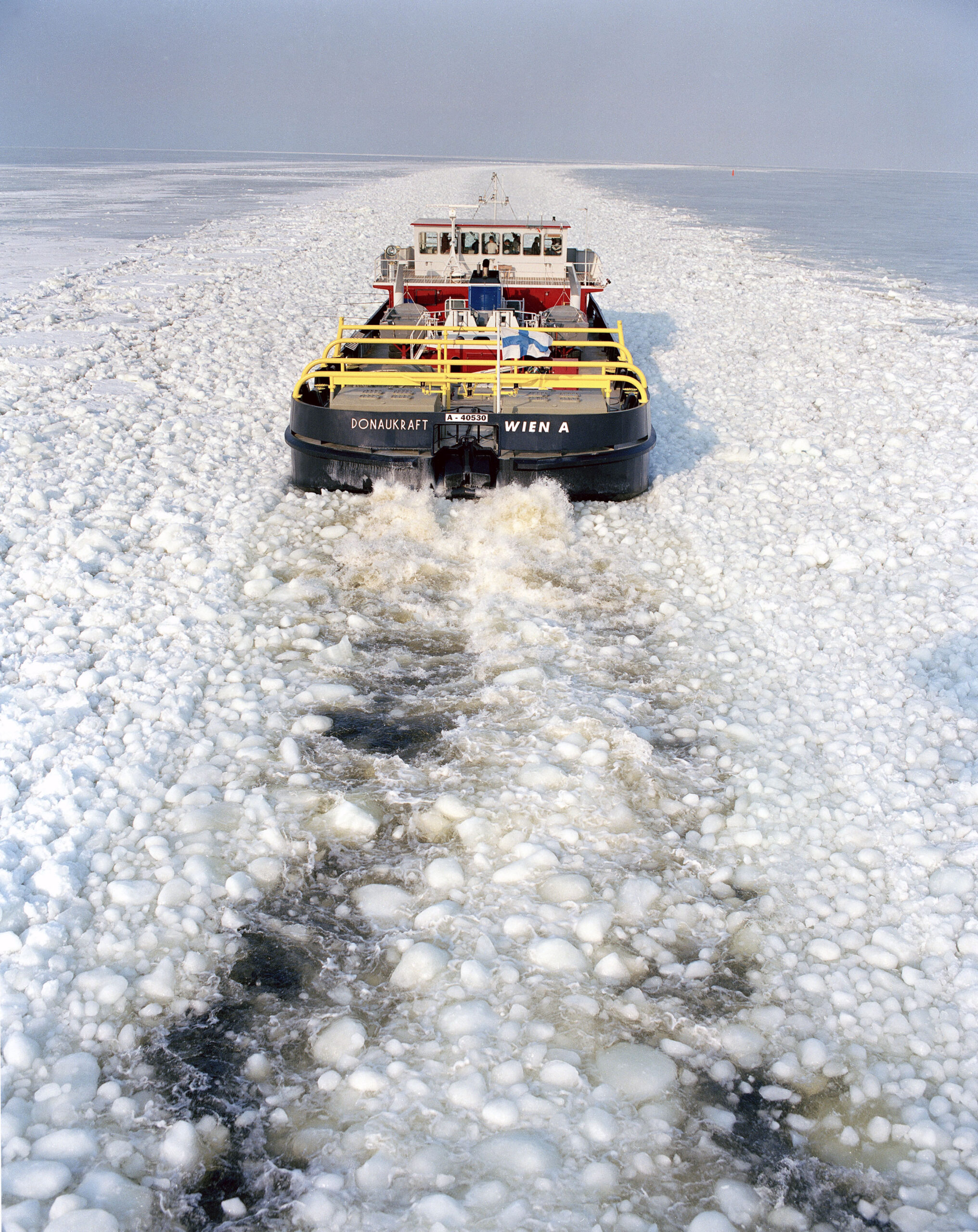
In a channel, each passing vessel breaks the insulating ice shield, leading to a heat loss from the water mass. This heat loss intensifies the ice formation as it increases the thickness of the ice sheet or the brash ice layer and creates even larger ice blocks hindering the flow of the traffic.
According to studies, the passing of four vessels a day may increase the ice formation five times higher than without any traffic. A snow cover adds the influence of navigation, since snow easily turns into slushy ice once it gets in touch with cold water. With each passing vessel pushing the brash ice to the sides, ice collars on both sides of the vessel grow, hindering navigation and increasing the risk of collisions.
“Thick brash ice in connection with shallow water can dramatically reduce propulsion efficiency, which results in poor vessel performance,” Lönnberg adds.
Half a century of expertise
The first shallow-draught river icebreakers designed by Aker Arctic’s predecessor were built in the 1970s. A more recent example is Röthelstein, delivered in 1995, a river icebreaker used on the Danube in Vienna, Austria, to ensure that water flows freely to the local hydro-power station. Her operational draught is only 2.0 metres, with excellent icebreaking capabilities and manoeuvrability.
In the mid-1990s, the two sister ships Arcticaborg and Antarcticaborg, were developed for the shallow Caspian Sea. Their draught is 2.9 metres, full speed over 13 knots with a bollard pull of 32 tonnes.
The most recent shallow-draught icebreaker built is the Mangystau-series of five vessels, constructed in 2010 and 2011. They were fully designed for independent year-round operations in the Northern Caspian Sea, an extremely shallow area, and have a minimum draught of 2.5 metres.
In 2022, Mangystau-2 was sold to the Government of Canada and renamed CCGS Judy Lamarsh.
Navigating shallow ice areas
Shallow-draught icebreakers are typically needed in specific areas where freezing conditions exist. Such areas include navigable rivers, shallow seas, estuaries, archipelagos, and lakes.
“These regions may not freeze every year but contain infrastructure that requires maintenance under all conditions, such as power stations or wind turbine installations,” Lönnberg explains.
“The smallest draught we have designed so far is 1.5 metres, but depending on the specific requirements, we might be able to design fully capable vessels with an even shallower draught,” he notes.
Customised solutions for unique environments
As each operational area is unique, there are no off-the-shelf solutions. Furthermore, many features effective on other types of icebreakers may not apply in shallow water, where the seabed is closer to the hull. Detailed research on local conditions is therefore always necessary when developing a new vessel design.
“Shallow water presents an additional challenge in the same way as freezing temperatures and must be considered from the onset of the design process,” Lönnberg underlines. “It is also essential to note that an icebreaker is inherently heavier than a similarly sized open-water vessel, due to increased power needs, fuel capacity, ice strengthening, and insulation.”
Sales Manager Arto Uuskallio adds that Aker Arctic’s expertise has evolved hands-on over the past five decades, based on extensive experience with shallow-draught icebreaker projects.
“Our experience in developing hull forms, structures, material selection, weight control, propulsion solutions, and weight supervision during construction is hard to match,” Uuskallio asserts.
Text by Catarina Stewen